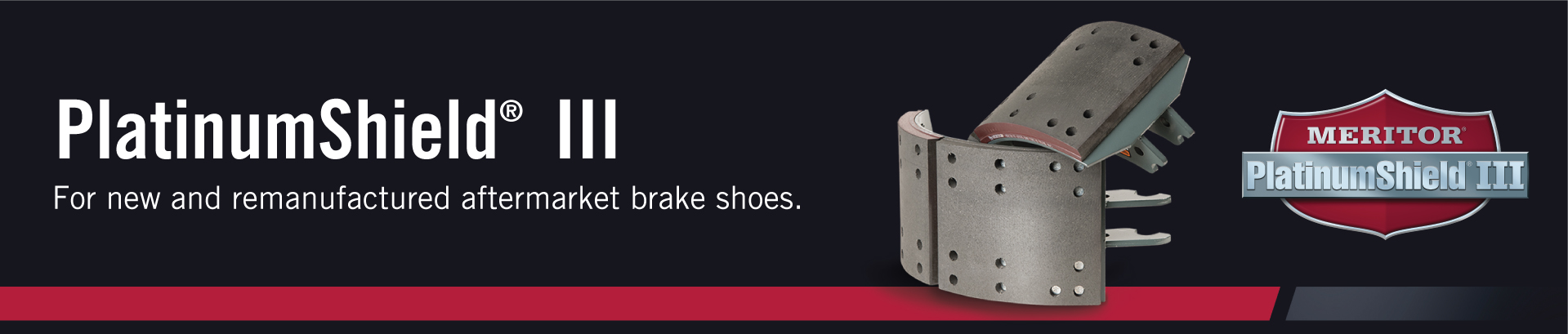

OUR “BRAKE-THROUGH” TECHNOLOGY IS NOW LONGER-LASTING TECHNOLOGY.
Our aftermarket engineering team discovered a refinement in the process that provides superior adhesion of the coating to the surface of the shoe. Superior adhesion enables the coating to protect the brake shoe for a significantly longer time on the road, increasing the shoe’s durability to withstand the corrosion caused by highway de-icing chemicals. The result is a quantum leap in technological performance that creates a new standard of brake-shoe durability. PlatinumShield III coating provides unsurpassed resistance to rust-jacking and corrosion while extending the life of your brakes.
As a result, Meritor new and reman brake shoes with PlatinumShield III coating deliver everything you expect from a worldwide brake leader, including our 3-Year/300,000-Mile warranty against rust-jacking.
Get Our New Extended Brake Shoe Life, Plus Reduced Stopping Distance (RSD) Friction Material.
No other brake shoe delivers extended protection from rust-jacking for the full brake life like Meritor brake shoes with PlatinumShield III coating. And no other brake shoe delivers such a combination of stopping power and corrosive protection, because Meritor brake shoes with PlatinumShield III coating now also feature new Meritor RSD friction materials. It’s simply the best combination of braking and durability available in the aftermarket.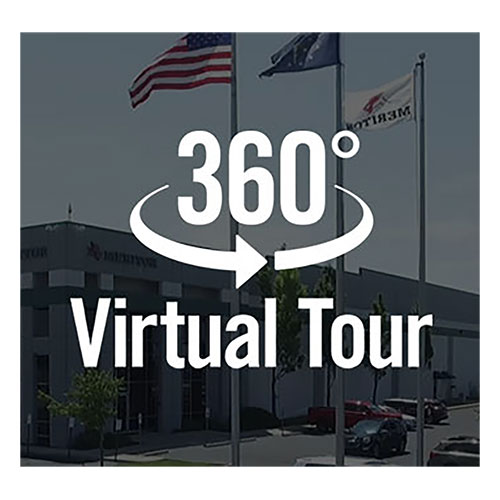
Our aftermarket engineering team discovered a refinement in the process that provides superior adhesion of the coating to the surface of the shoe. Superior adhesion enables the coating to protect the brake shoe for a significantly longer time on the road, increasing the shoe’s durability to withstand the corrosion caused by highway de-icing chemicals. The result is a quantum leap in technological performance that creates a new standard of brake-shoe durability. PlatinumShield III coating provides unsurpassed resistance to rust-jacking and corrosion while extending the life of your brakes.
As a result, Meritor new and reman brake shoes with PlatinumShield III coating deliver everything you expect from a worldwide brake leader, including our 3-Year/300,000-Mile warranty against rust-jacking.
Get Our New Extended Brake Shoe Life, Plus Reduced Stopping Distance (RSD) Friction Material.
No other brake shoe delivers extended protection from rust-jacking for the full brake life like Meritor brake shoes with PlatinumShield III coating. And no other brake shoe delivers such a combination of stopping power and corrosive protection, because Meritor brake shoes with PlatinumShield III coating now also feature new Meritor RSD friction materials. It’s simply the best combination of braking and durability available in the aftermarket.
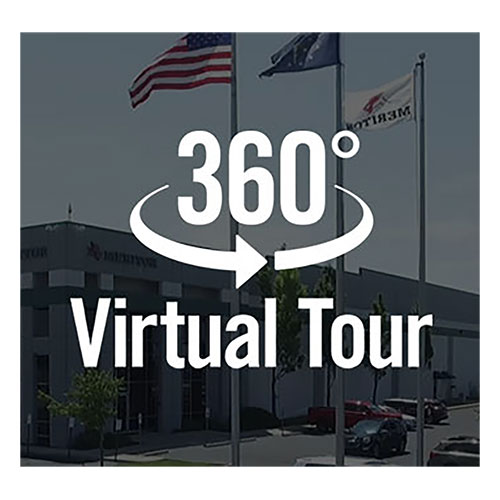
Plainfield, IN facility
TAKE A TOURRUST JACKING

WHY DOES RUST-JACKING REQUIRE A LONG-LASTING SOLUTION?
- Rust-jacking often shortens the life of brake shoes and brake linings, preventing truck operators from getting the full life out of their equipment.
- Rust-jacking is a field condition caused by harsh anti-icing liquids in winter road solvents, combined with thawing and freezing moisture that penetrates the brake shoe coating and causes rust to build up on the brake shoe table.
- As rust builds up, it pushes outward against the lining, “jacking” it up between the rivets, until the lining cracks.
- Once the lining cracks, driving is unsafe, and the lining must be replaced, cutting short the brake shoe life and denying truck operators its full value – often with a thick amount of lining remaining.
- Rust-jacking is found most often where intense brake heat cannot dry out the shoe table. Typically, it occurs in front shoes.
THE REMAN PROCESS
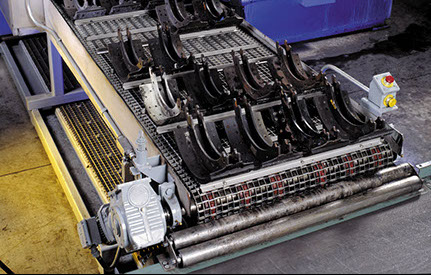
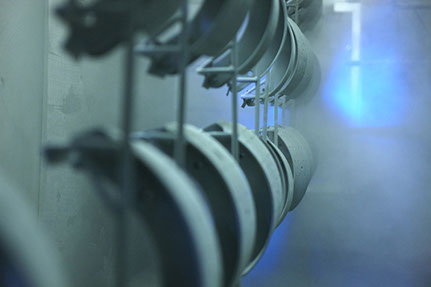
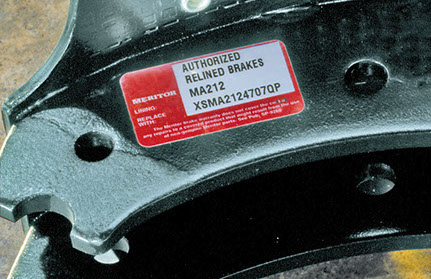
NINE-STEP REMANUFACTURING PROCESS
Meritor remanufactured brake shoes with PlatinumShield III coating offer all the advantages of the proven Meritor nine-step remanufacturing process, and greater adherence to the reman shoe surface. In our Plainfield, Ind., facility, each shoe is completely remanufactured − not rebuilt − and restored to the same high quality performance standards as those of original Meritor production brake shoes.
Step 1 – Initial Inspection
Trained technicians thoroughly inspect the core for excessive wear or damage, including broken welds, work cams and anchor slots.
Step 2 – De-Lining
Old lining is removed using a punch process to ensure the quality of the rivet hole for remanufacturing.
Step 3 – Cleaning
Grease and other contaminants are cleaned from the shoe through a baking process.
Step 4 – Shot Blasting
Removes remaining residue of contaminants.
Step 5 – Coining
Returns the brake shoe table to true original shape and dimensions.
Step 6 – Coating/Painting
All brake shoes based on friction material go through a coating and/or painting process. For all frictions except EG/EG2 and Fras-le AF520/AF523, the shoes run through a five-stage pre-treatment and drying process prior to the coating of the shoe with PlatinumShield III. The coating is then cured to ensure proper thickness and consistency across all shoes. All EG/EG2 and Fras-le AF520/AF523 shoes are dipped in water-soluble black paint.
Step 7 – Riveting
Top-quality brake linings are riveted to the brake shoes using a hydraulic riveting process, to ensure consistent performance.
Step 8 – Quality Inspection
Every Meritor remanufactured brake shoe receives a thorough inspection before being cleared for shipping.
Step 9 – Label Approval
Only remanufactured brake shoes with rust-jacking coating that pass the rigorous inspection process receive a brake shoe label.
Meritor remanufactured brake shoes with PlatinumShield III coating offer all the advantages of the proven Meritor nine-step remanufacturing process, and greater adherence to the reman shoe surface. In our Plainfield, Ind., facility, each shoe is completely remanufactured − not rebuilt − and restored to the same high quality performance standards as those of original Meritor production brake shoes.
Step 1 – Initial Inspection
Trained technicians thoroughly inspect the core for excessive wear or damage, including broken welds, work cams and anchor slots.
Step 2 – De-Lining
Old lining is removed using a punch process to ensure the quality of the rivet hole for remanufacturing.
Step 3 – Cleaning
Grease and other contaminants are cleaned from the shoe through a baking process.
Step 4 – Shot Blasting
Removes remaining residue of contaminants.
Step 5 – Coining
Returns the brake shoe table to true original shape and dimensions.
Step 6 – Coating/Painting
All brake shoes based on friction material go through a coating and/or painting process. For all frictions except EG/EG2 and Fras-le AF520/AF523, the shoes run through a five-stage pre-treatment and drying process prior to the coating of the shoe with PlatinumShield III. The coating is then cured to ensure proper thickness and consistency across all shoes. All EG/EG2 and Fras-le AF520/AF523 shoes are dipped in water-soluble black paint.
Step 7 – Riveting
Top-quality brake linings are riveted to the brake shoes using a hydraulic riveting process, to ensure consistent performance.
Step 8 – Quality Inspection
Every Meritor remanufactured brake shoe receives a thorough inspection before being cleared for shipping.
Step 9 – Label Approval
Only remanufactured brake shoes with rust-jacking coating that pass the rigorous inspection process receive a brake shoe label.
TESTING
PlatinumShield III
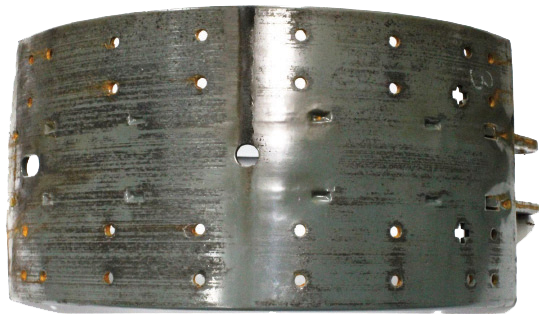
Competitor H
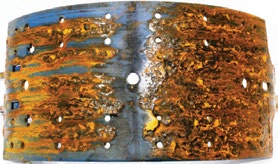
Results after a 400-hour ASTM B-117 salt spray test
CORROSION RESISTANCE TESTING OF PLATINUMSHIELD III VS. A COMPETITOR.
Meritor engineers recently conducted a competitive corrosion-resistance benchmark evaluation between PlatinumShield III coating and a competitor’s corrosion-resistant shoe coating. Both shoes were salt spray tested for 400 hours per ASTM B-117 to measure corrosion resistance. Results can clearly be seen in the post-testing photos. The superior performance of the PlatinumShield III coating resulted in a corrosion rating of 9 on the ASTM scale, while the competitors corrosion-resistant shoe coating rated 1 on that scale.
With PlatinumShield III, we’ve completely changed expectations for brake shoe life. In fact, PlatinumShield III meets our desired criteria:
- It rates higher than 8 on the ASTM scale.
- Meritor brake shoes with PlatinumShield III coating offer an industry-leading full 3-Year/300,000-Mile warranty against rust-jacking.
Our proprietary PlatinumShield III coating is available on new and remanufactured Meritor and Fras-le® brand brake shoes.
- Rust-jacking is a field condition caused by harsh anti-icing liquids in winter road solvents, combined with thawing and freezing moisture that penetrates the brake shoe coating and causes rust to build up on the brake shoe table.
- As rust builds up, it pushes outward against the lining, “jacking” it up between the rivets, until the lining cracks.
- Once the lining cracks, driving is unsafe, and the lining must be replaced, cutting short the brake shoe life and denying truck operators its full value – often with a thick amount of lining remaining.
- Rust-jacking is found most often where intense brake heat cannot dry out the shoe table. Typically, it occurs in front shoes.
WARRANTY
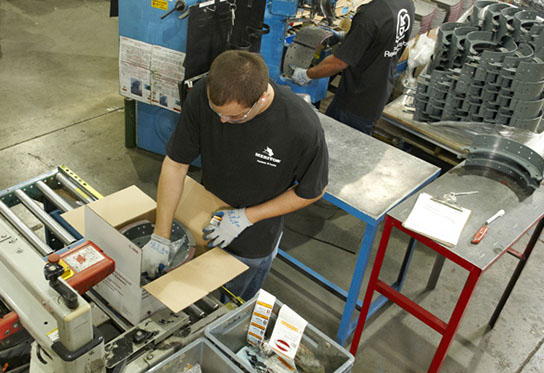
Extended Protection Against Rust-Jacking, And Longer Wheel-End Coverage
PlatinumShield III coating for new and remanufactured Meritor brake shoes not only provides coverage against rust-jacking for 3-Years/300,000-Miles, but also positively impacts wheel-end extended warranty coverage for both trucks and trailers. When you purchase and install complimentary Meritor wheel-end products together, you can get a 5-Year/Unlimited-Mileage wheel-end extended warranty. See the coverage overview below or visit MeritorPartsWarranty.com for full coverage details and registration.
PlatinumShield III coating for new and remanufactured Meritor brake shoes not only provides coverage against rust-jacking for 3-Years/300,000-Miles, but also positively impacts wheel-end extended warranty coverage for both trucks and trailers. When you purchase and install complimentary Meritor wheel-end products together, you can get a 5-Year/Unlimited-Mileage wheel-end extended warranty. See the coverage overview below or visit MeritorPartsWarranty.com for full coverage details and registration.
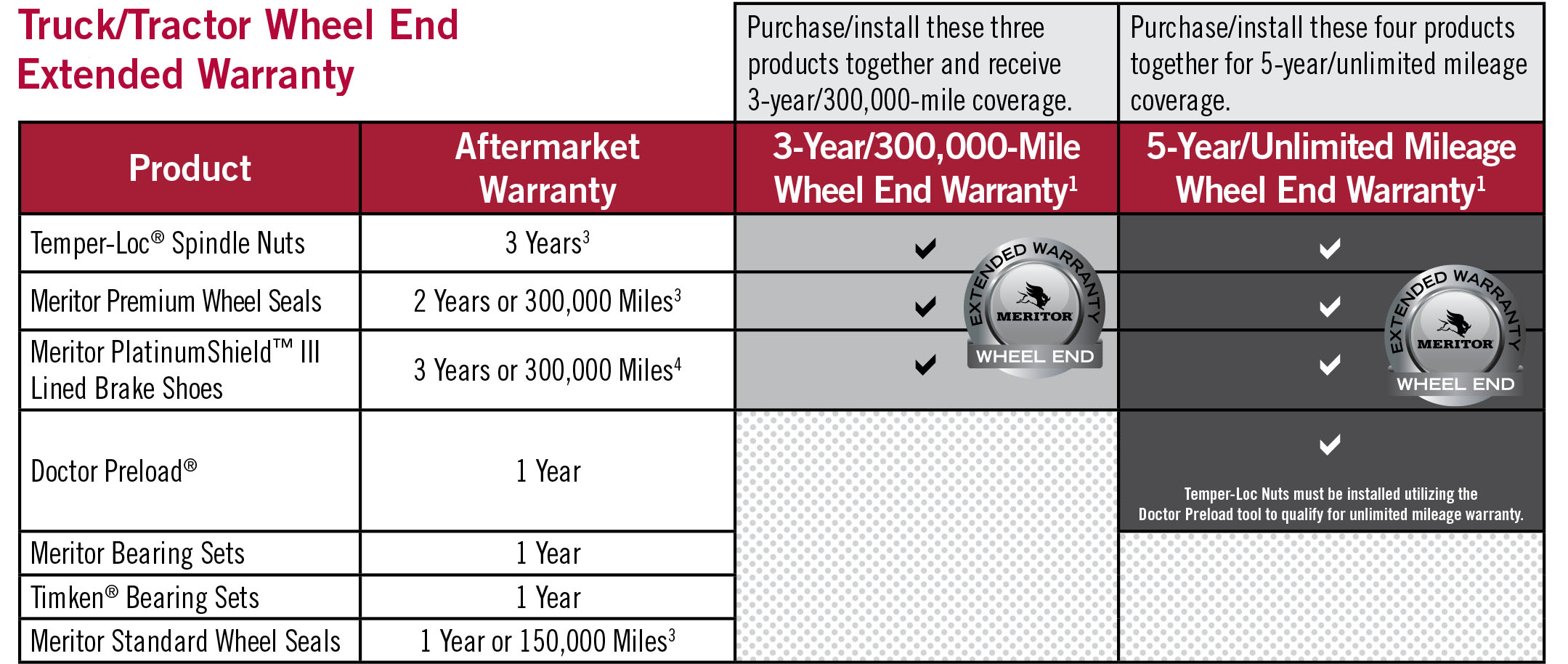
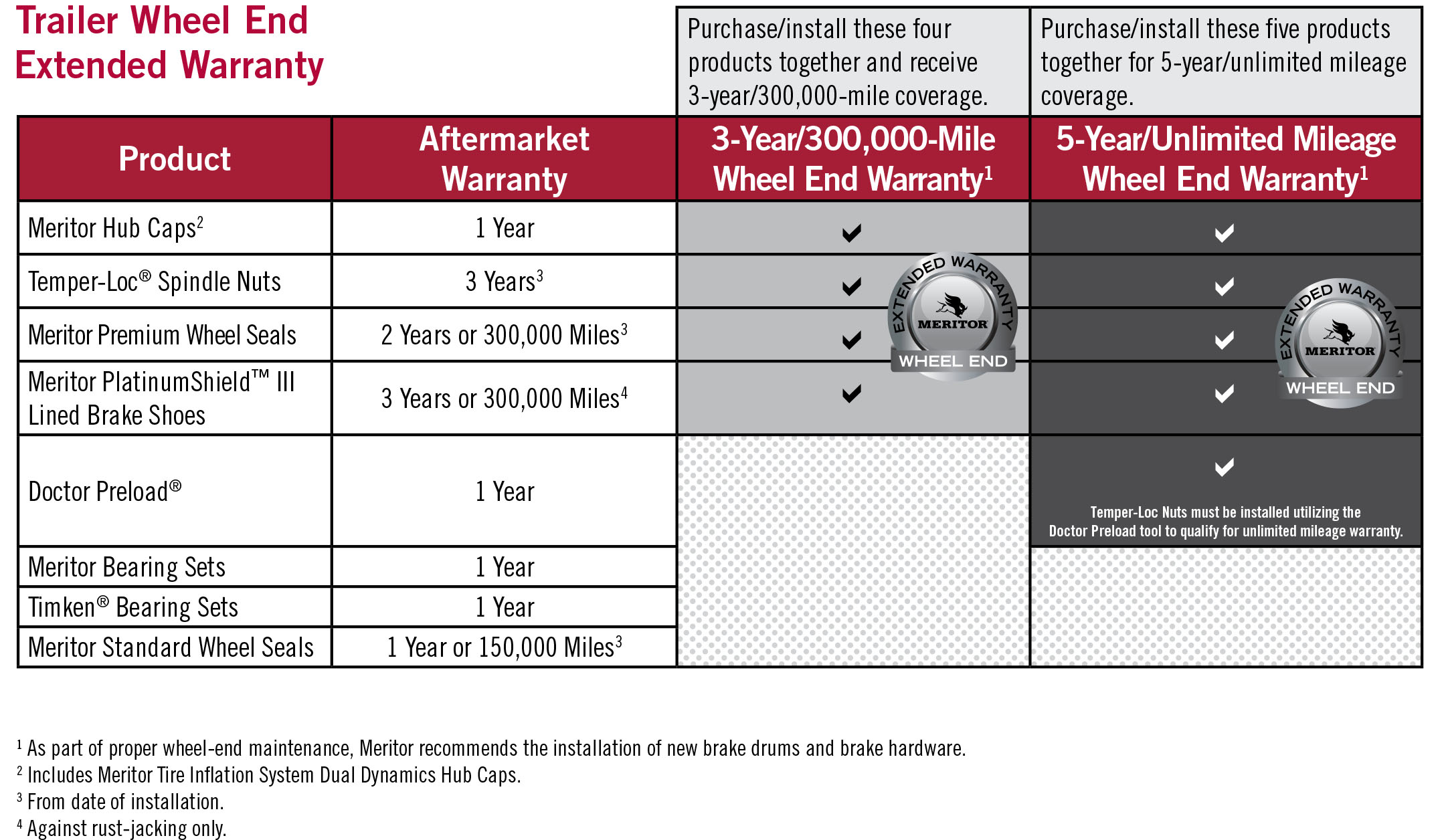